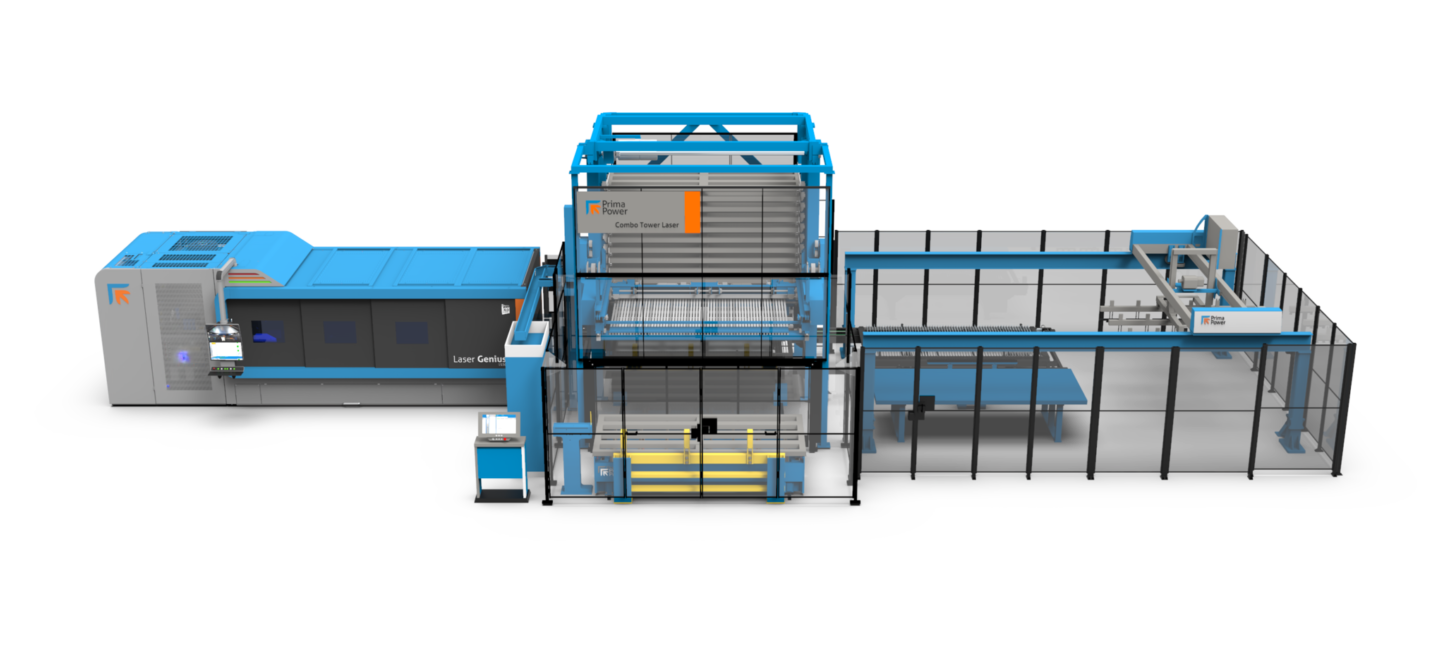
For 2D laser cutting, Prima Power displays for the first time at a German fair Laser Genius+, the innovative 2D machine totally Made in Italy with unique high-tech solutions, allowing high levels of performance, efficiency, quality, ease of use, automation and intelligence. Thanks to the high dynamics (180 m/min trajectory speed, 2.8 g acceleration) and precision of the machine, cycle times are considerably reduced and productivity and cutting quality are strongly increased. With the wide range of laser powers available and the machine features designed to have total control over the laser process and to obtain maximum reliability and quality from the power at hand, customers can get the best return on investment, based on their real needs.
Laser Genius+ is a “plug & play” compact machine where all services, already tested, are integrated into one dedicated module separated from the machine work area, with very fast installation times (ready to cut in 2 days) and thanks to a symmetrical and reversible layout, it can be inserted in any production context. In addition, with its small footprint Laser Genius+ allows highly efficient use of space. Despite its compact layout, the Laser Genius+ has the largest working area compared to other 2D machines available on the market (X, Y axis strokes: 3150 x 1600, for the 1530 model, 4320 x 2200, for the 2040, and 6320 x 2200 for the 2060).
Ease of use is another advantage of Laser Genius+ that is priceless. The machine is incredibly user-friendly and smart with two 24” full HD monitors a 4K video camera, on-board software modules simplifying nesting and technology, sensors and artificial intelligence algorithms for advanced process monitoring and control features. It ensures the highest levels of ergonomics and accessibility also due to the sliding doors which can be placed on the right or left side, or even on both sides.
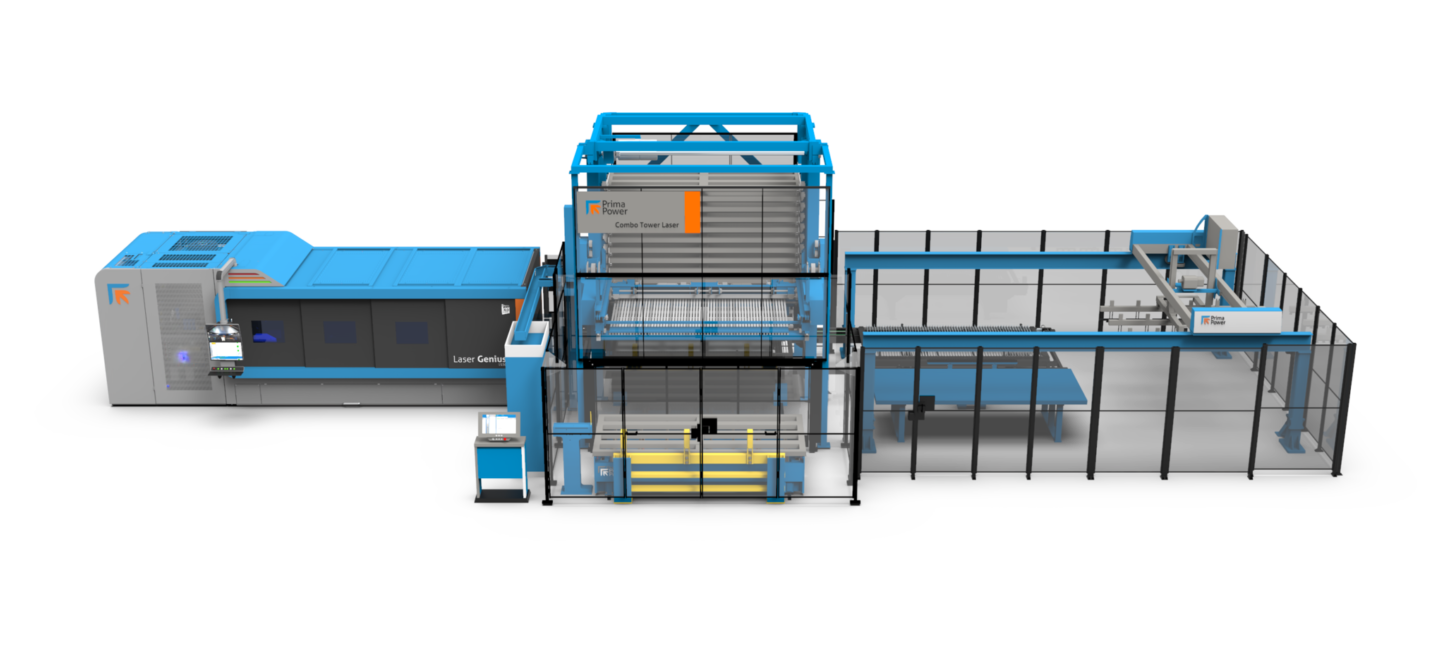
Laser Genius+ can be easily connected to the whole range of Prima Power automation systems. At Blechexpo it is exhibited with Combo Tower Laser and the new, clever and flexible picking and stacking robot PSR 2D by Prima Power, an efficient solution for managing the material flow which automates part picking and stacking in a fast and flexible way. PSR stacking accuracy is high and intervals between stacks minimal, allowing optimal usage of stacking area, automatically. Thanks to the modular structure of the system and Prima Power wide product portfolio, PSR 2D can be connected directly to the Night Train FMS storage solution. Automatic panel bender can also be connected to PSR 2D creating an automated production line from raw sheet metal to cut and bent finished products.
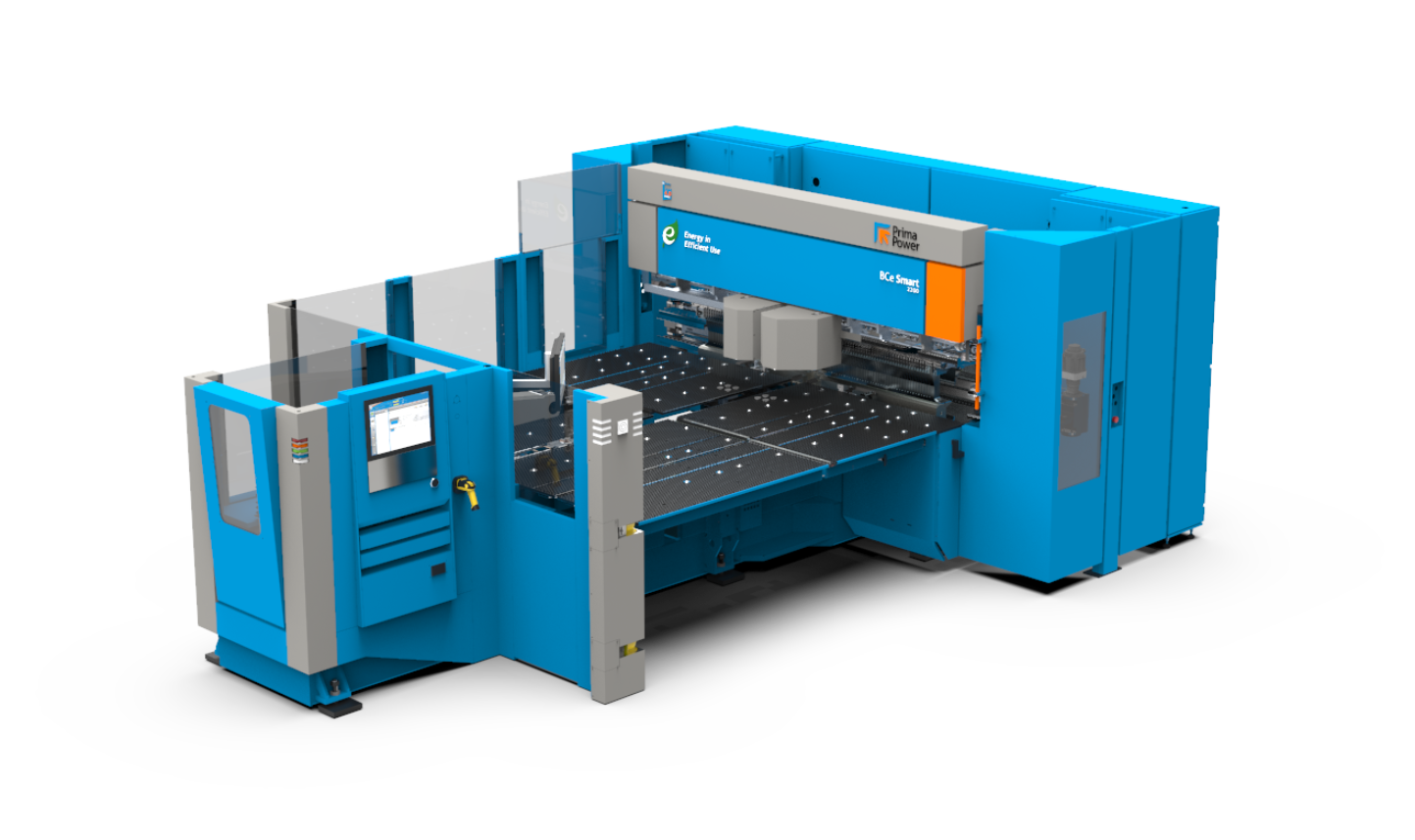
Prima Power BCe Smart bending cell is also showcased at Blechexpo. It is a servo-electric machine, designed for customers looking for a flexible and semi-automatic panel bender with a “safety integrated” concept that allows the operator to focus only on value-added operations, aided by visual devices and sound signals. Maximum comfort for the operator is achieved thanks to two laser scanners, instead of physical barriers, and worktable tops that can be lowered to facilitate the loading of small or medium-sized parts. The machine’s compact layout and combined loading and unloading sequence guarantee high productivity.
BCe Smart comes equipped with two innovative technologies for the bending quality control like DABA and API, allowing getting the most precise bent components. DABA (Dynamic Adjustment of the Bending Angle) is a proprietary technology that considerably reduces the time required to create a new panel, thanks to corrective parameters suggested in relation to several material variables. API (Advanced Profile Inspection) is a complementary patented option that consists of a camera device used to apply corrections to a bend in order to reach the target angle within the required tolerance.
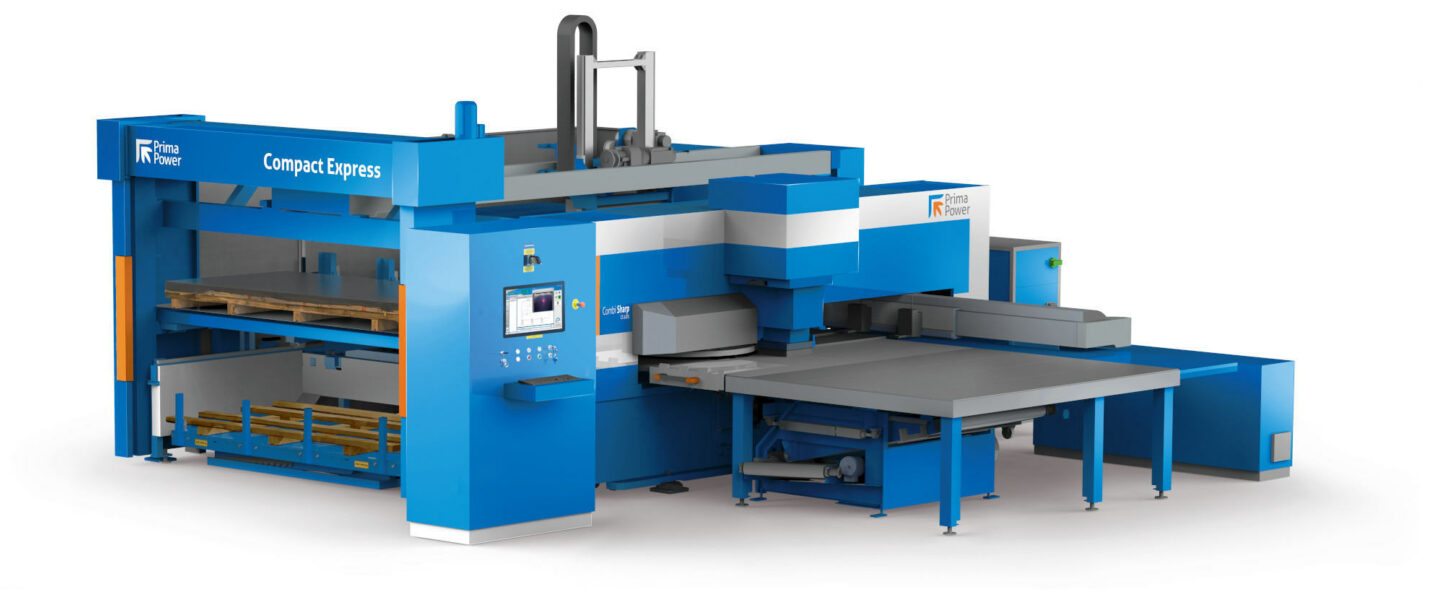
Flexible by definition, the Prima Power line of combined punch+laser systems is also present at the Blechexpo. In particular, visitors can see the Combi Sharp in action, the compact servo-electric model which provides outstanding energy efficiency, low maintenance requirement and a high speed of operation. The smart integration of different technologies allow to have punching, forming, marking, bending, laser cutting - all in one machine. The cornerstones of the machine’s productivity include large tool capacity (up to 384 standard or 128 index tools), a wide range of special tools available and easy and fast setup change.
The Combi Sharp is equipped with a range of highly efficient fiber laser, a perfect match for the system’s intrinsic flexibility and sustainability. The machine reduces the manufacturing cost per component, is suitable for any batch size and, thanks to its versatility, there’s virtually no limit to part design and complexity.
Due to its compact construction the automated Combi Sharp does not require much more floor space than the machine itself, but it dramatically increases productivity. At Blechexpo the machine is equipped with the Compact Express, the fully automated material handling device featuring several combinations of automatic and manual loading and unloading cycles.

A proprietary, common software is fundamental to grant that “all sides of performance” are perfectly and simply managed, connected, and controlled in a fully integrated digital factory. Live demonstrations of Prima Power software for smart manufacturing are available for visitors to experience how a single module can schedule and monitor the whole manufacturing process, all technologies involved, and all levels of automation. Prima Power, as one-stop-supplier owning and controlling all elements involved in the manufacturing process, can help customers manage its production in a fully integrated and interconnected mode. This allows a considerable increase of efficiency and productivity and a drastic reduction of working times.
At Blechexpo Prima Power is showing all its software packages to support different levels of production automation. From the single automation of information flow to the fully automated lights out operation, from the static nest-driven production to the constantly varying mass production – all possible manufacturing requirements are efficiently covered with Prima Power software.