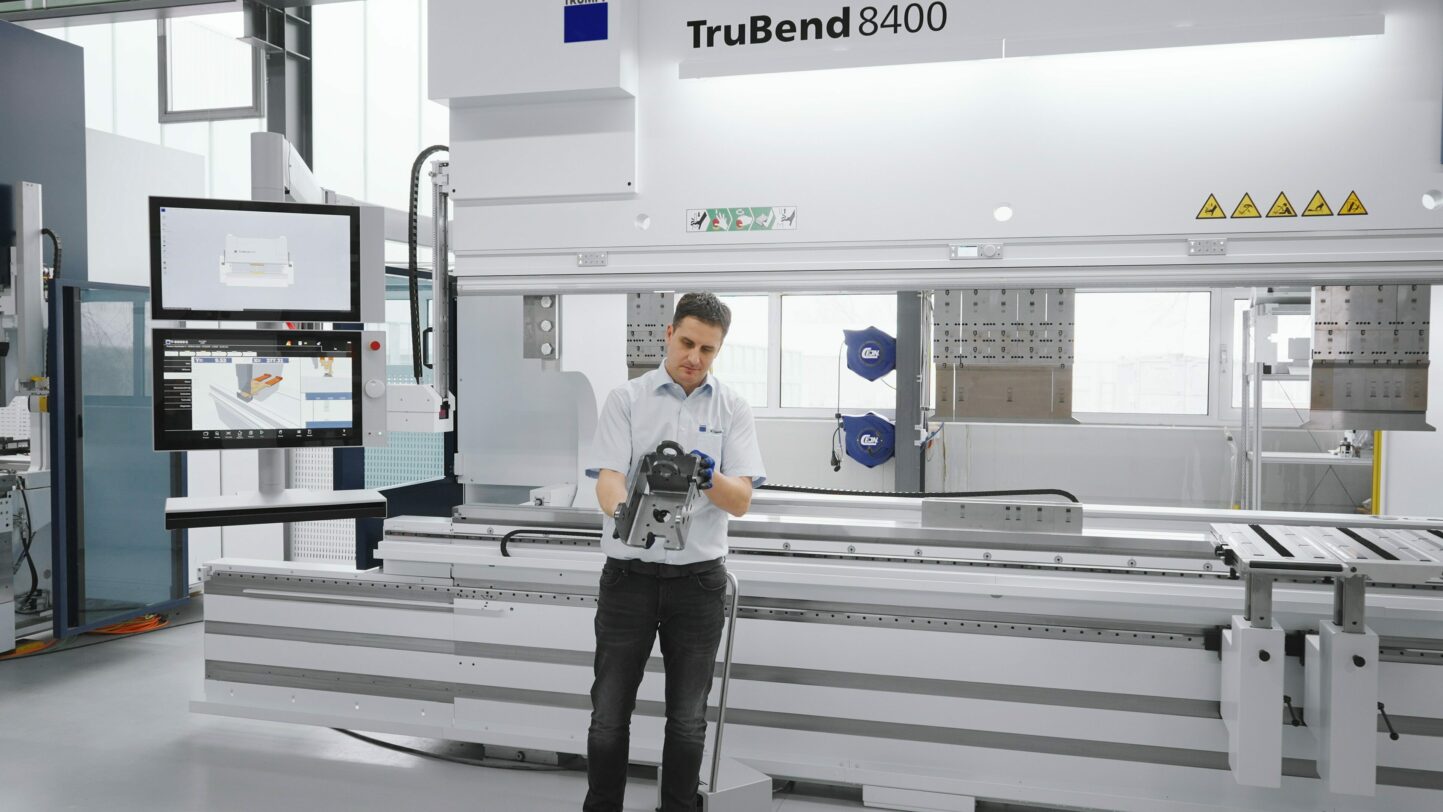
High-tech company TRUMPF used the recent INTECH in-house trade show as an opportunity to showcase the latest generation of its TruBend Series 8000. With an 880-millimeter open height and a stroke of 700 millimetres, the TruBend 8000 bending machine offers a superbly efficient way to bend very large parts, allowing workers to easily bend and remove workpieces that require a large box height.
It also provides numerous optional extras designed to facilitate the bending of heavy parts. These include a bending aid that makes operators’ lives easier by automatically positioning the workpiece for bending. This series of machines can also be equipped with a special tool clamp for XXL parts. “The new TruBend Series 8000 is the perfect addition to our portfolio of bending solutions. Whatever their bending application, companies can rely on TRUMPF to have the technology they need – from entry- level machines to fully automated solutions for oversize formats,” says product manager Deborah Lidauer.
The best way to bend high-tensile steels
With a press force of 400 metric tons, the first in this new generation of machines is an efficient powerhouse that has no trouble processing short, thick pieces of sheet metal. But thanks to its generous 4.40-meter bending length, it is equally at home with longer, thinner parts. The machine is also suitable for bending high- tensile materials such as Hardox or Weldox engineering steels. Station bending is another option available with the TruBend 8000. By moving workpieces from one station to the next, each equipped with different upper and lower tools, workers can tackle a range of parts and bending operations without having to change the machine setup for each operation. This makes the TruBend 8000 particularly suitable for companies that bend large parts in small batches, including fabricators in the vehicle manufacturing, mechanical engineering, and building-services sectors. This model is also a great choice for general-purpose work in job shops.
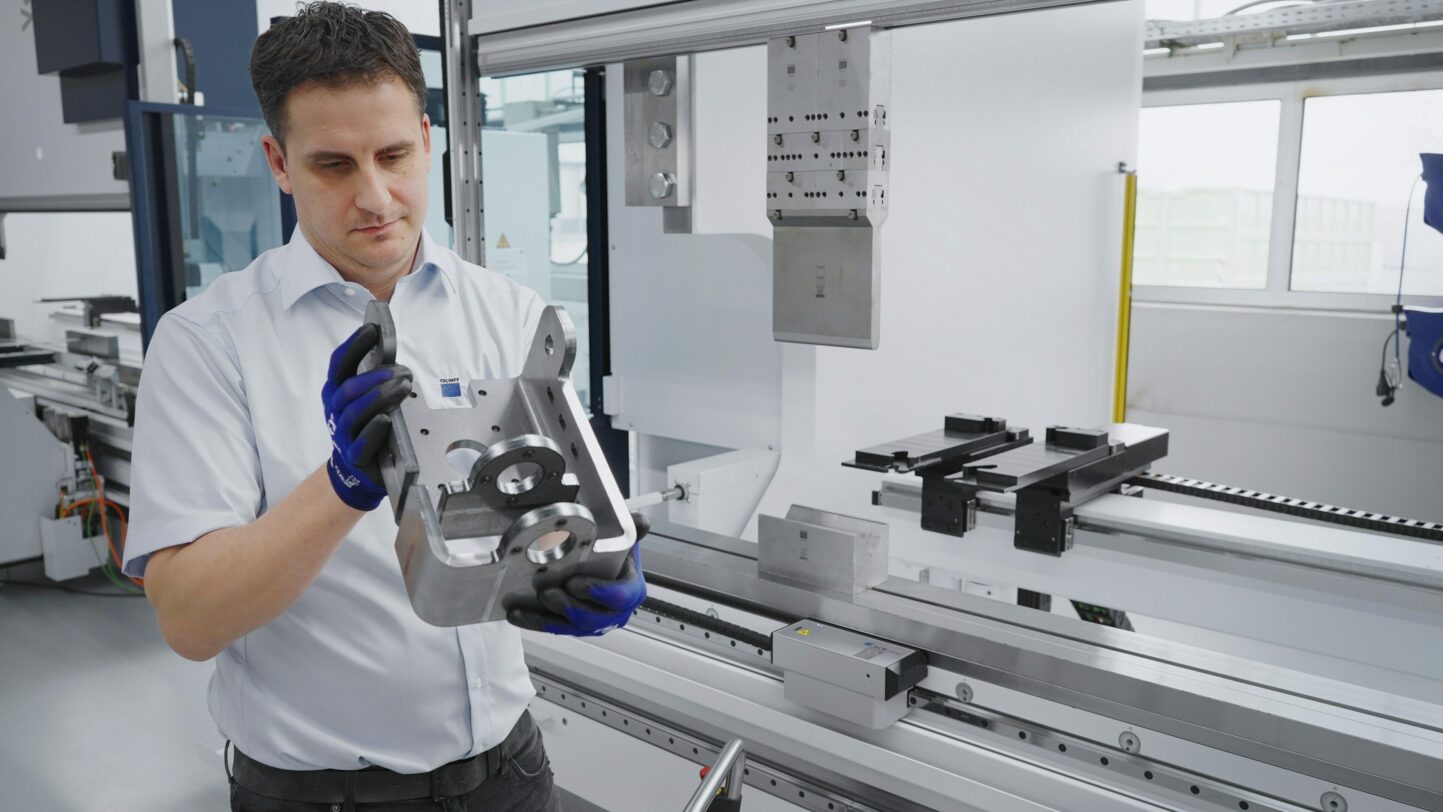
Automation and sustainability
Its numerous automation functions make the TruBend 8000 a suitable candidate for use in a smart factory. The most advanced version includes features for fully automated operation provided by TRUMPF partner Starmatik. These include a six-axis industrial robot that handles loading and unloading. Moreover, the use of a robot allows downstream processing steps to be integrated in the automation system, such as forming, joining, and welding. The TruBend Series 8000 also comes with TRUMPF’s tried-and-tested Boost and TecZone Bend bending software for offline programming. The machine operator simply uploads a 2D or 3D model of their part into the program. The software then independently creates a 3D simulation including collision monitoring, which the operator can then adopt for the bending process, either in its entirety or with minor manual changes. TruBend 8000 machines are also designed to facilitate the trend toward greater sustainability in manufacturing. Users can choose to equip their machine with an on-demand drive, which automatically adjusts the motor’s revolution speed to the movement of the press beam. As well as limiting noise generation, this feature can also reduce energy consumption by up to 26 percent.
TruBend 8000
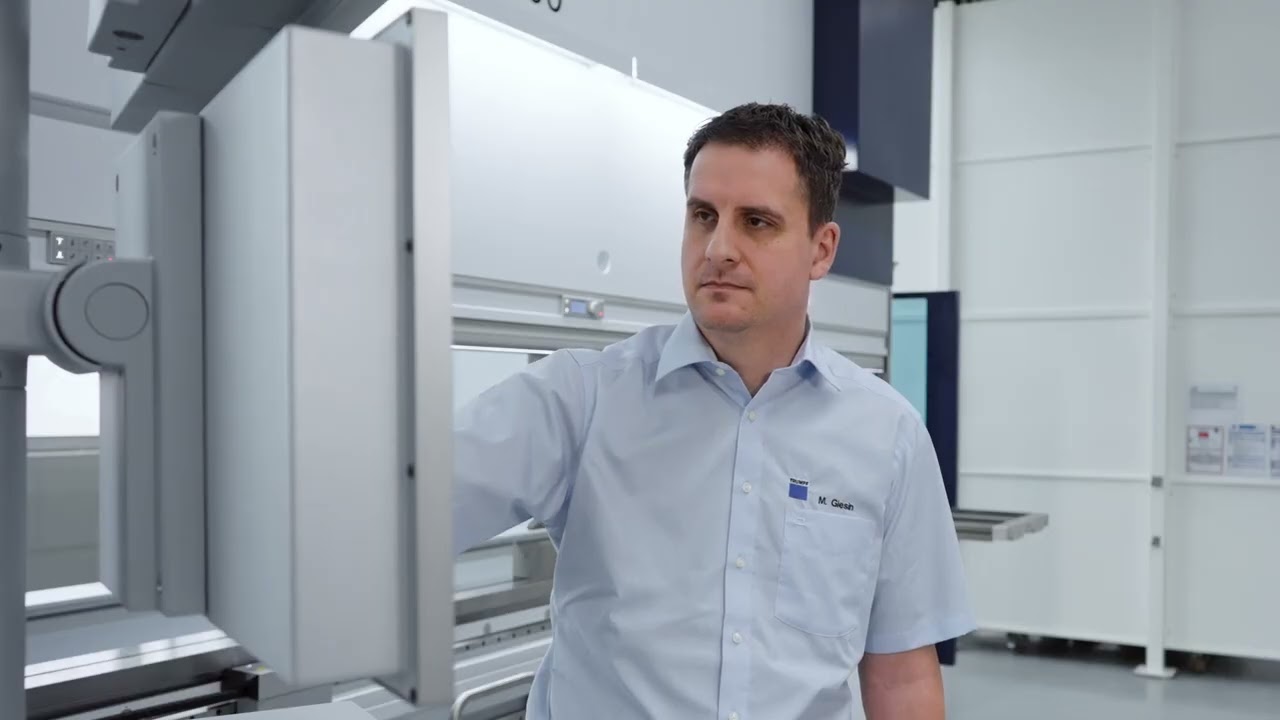