Automatic set-up and tool change are the two most valuable assets of B3.AU-TO, the Salvagnini press brake. Designed by combining the best features of the electric and hydraulic solutions, the B3.AU-TO significantly extends the availability, autonomy, and flexibility of the press brake.
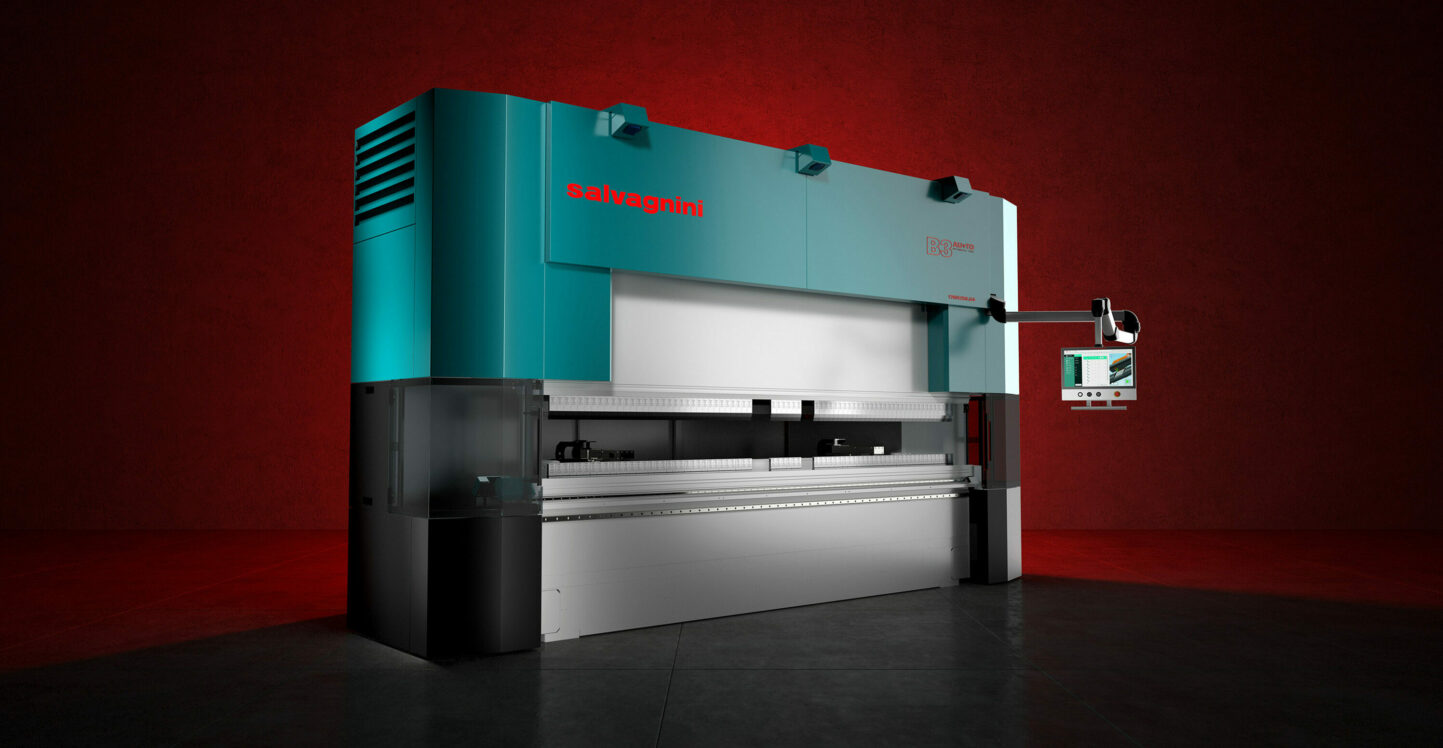
The Salvagnini B3.AU-TO press brake relieves the pressure on companies dealing with manual tool set-up time and downtime for feeding, programming, part manipulation and controls. Available in four models, with bending lengths up to 3 or 4 meters and a maximum force of 170 or 220 tons, the Salvagnini B3.AU-TO enables companies to better cope with a dynamic market, which demands increasingly smaller batches, kit productions or batch-ones with very short lead times. The AU-TO automatic tool change device and the ATA automatic tool adjuster, which adjusts the length of the stations, significantly reduce the press brake re-tooling, increasing autonomy and productivity, and reducing the lead time.
Distinctive features of the B3.AU-TO include the Salvagnini-patented upper and lower automatic tool change unit. Additionally:
- AU-TO reduces set-up times and increases the availability of the press brake. The operations are rapid and in cycle, even in masked time, helping to increase the efficiency of the press brake.
- B3.AU-TO has the smallest footprint on the market. The tool store is covered and located in the rear part of the B3. It can contain up to 24 meters of tools up to 1000 mm in length without segmentation.
- AU-TO makes the most out of the ATA devices, which automatically adjust the upper and lower bending tool length, saving time, and increasing production efficiency.
- AU-TO assures full flexibility for tools because the press brake allows mixed tooling: after the automatic tool change and set-up, the B3.AU-TO allows the manual integration of standard WILA tools or special tools, such as hemming tools, on the bend line.
B3 equals precision. All the B3 press brakes are equipped with the following four precision features:
- MAC3.0 – a set of integrated adaptive technologies that make the system intelligent and cancel out waste and corrections.
- S-Crowning – the mechanical crowning system that ensures consistent bending angles along the entire bending length: as the parameters – material, thickness, length, and therefore the required bending force – change, the effective curvature of the lower table is measured and compensated in real-time, without any operator intervention.
- TFC2.0, Total Frame Control, prevents deviations in the bending angle using an algorithm derived from the FEM study of each model. TFC2.0 compensates any in-cycle deformations of the press brake structure according to the variations in the characteristics of the part being processed.
- AMS is a laser angle measurement system that detects and corrects variations in the bending angle due to sheet metal spring back. Regardless of the length of the press brake and of the part being bent, the angle is always measured in one single point: this approach helps reduce the cycle time without compromising on precision.
All these features make the B3.AU-TO the ideal press brake for companies with a high daily item turnover rate. The AU-TO and ATA devices reduce the cycle time, making it easier to forecast, plan and monitor. The direct consequence of integrating the B3.AU-TO into your production cycle is greater process efficiency and greater reactivity, which turns into greater daily productivity and therefore higher profitability.
Additional B3 highlights
Impacts Is the new environmentally focused tool that measures the consumption of electricity on the B3 press brake. It is the first step towards calculating volumes of CO2 equivalent of each single manufactured component. Impacts is used to monitor and become aware of your consumptions, to optimise and reduce them. It increases profitability because reducing consumption means reducing running costs.
Maximum ram speed B3 is a hybrid press brake: it achieves the typical tonnages of hydraulic press brakes, with the speed of the electric ones. The technical solution that controls the ram movements is the Direct Drive: two independent direct-drive brushless motors, activated only when needed, allow the ram to reach fast approach and fast return with speeds up to 250 mm/sec depending on the chosen B3 model.
KERS for sustainable bending KERS is a proprietary Salvagnini system that recovers energy waste and reuses it in subsequent operations, accelerating and reaching higher speeds with the same consumption.
Maximum safety Every B3 with automation devices is equipped with radars to ensure ultra-high safety standards. Without physical barriers to protect the bending area during automatic set-up, these ultra-high frequency radars detect any movement in the safety area: they can detect human breathing - even when trying to stand still, an operator will always be detected - and exclude objects from detection - a stool, a metal sheet on the front sliding shelves, a pedal set, etc.
Ease of use FACE is the Salvagnini HMI for the whole product range, with the same look and feel for all technologies. FACE reduces the time required for interaction, as each function is immediately clear and available in just a few clicks. In addition to conventional numerical programming, FACE also allows graphic programming with PRESSTUDIO.
Office software for top efficiency B3 can be programmed on the machine, but programming in the office is what maximises its efficiency: the STREAMFORMER software automatically creates the bending sequence and set-ups, integrating perfectly with the AU-TO and ATA devices, enhancing the performances. Programming in the office also increases productivity, as while the programmer deals with the programs in the office, the operator continues to bend. The main objective is to minimize waiting times, making the press brake as efficient as possible.
Optimizing re-tooling with the software PARTS and STREAMFORMER are used to automatically program the parts in a job list, reducing the number of re-toolings between different programs. OPS, the modular production management software, has a function that automatically optimizes the part production sequence to minimize overall re-tooling times.